Why are HDPE Pipes Preferred?
Examining the Advantages Driving Adoption of High-Density Polyethylene Piping
High-density polyethylene (HDPE) piping has gained increased preference for municipal, industrial, agricultural, and utility service applications. What are the key advantages driving the growing use of HDPE pipe systems over traditional materials? This article examines the benefits leading to its preferred status.IFAN factory with 30+ years of manufacturing experience supports color/size customization and free samples. Welcome to consult for catalog and free samples. This is our Facebook Website: www.facebook.com.
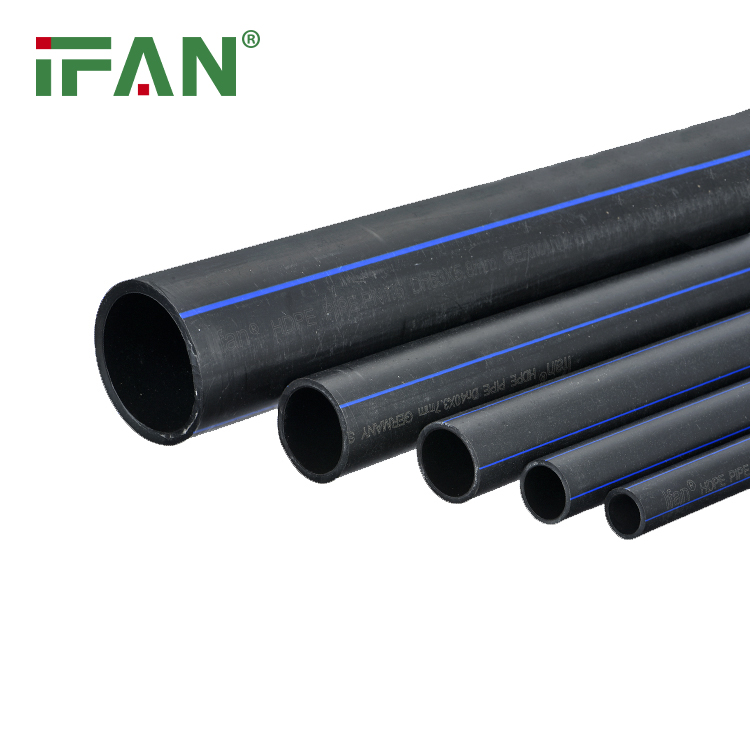
Corrosion Resistance
HDPE pipe offers complete corrosion resistance and immunity to galvanic and electrolytic attacks. HDPE will not corrode in soils or waters across the entire pH range.
- HDPE requires no cathodic protection versus steel pipes needing heavy coatings.
- HDPE remains inert even to salty seawater or brine fluids that rapidly degrade other materials.
- HDPE lasts indefinitely regardless of soil or water conditions.
This corrosion resistance minimizes maintenance needs and maximizes service life. In corrosive environments, HDPE is clearly preferred.
Light Weight Compared to Iron, Concrete, and Steel
At under 5% of the density of steel, HDPE pipe is much lighter per foot of piping. This provides key advantages:
- Easier handling and installation with reduced heavy equipment needs.
- Cost savings in transportation from factory to site.
- Allows use in floating marine pipes that steel would sink.
- Enables installation in areas inaccessible to heavy pipe materials.
The lightweight, fatigue-resistant HDPE reduces construction complexity and expense.
Long Continuous Pipe Lengths
Typical HDPE pipes can be supplied in coiled lengths up to 50 feet or straight lengths up to 40 feet. This significantly reduces number of joints needed compared to 20-foot steel, ductile iron, or PVC lengths.
- Fewer joints speed up installation with less labor.
- Complete PE fusion welds are stronger than gaskets or couplings.
- Long sections allow snaking in buried applications.
- Large-diameter reels remain transportable.
By minimizing connections, overall piping system integrity and reliability are enhanced.
Flexibility and Fatigue Resistance
HDPE pipe remains flexible even at sub-freezing temperatures. It can elongate and bend without damage. This enables unique installation options:
- Snaking trenches in remote areas follow land contours.
- Pipe deformation absorbs ground shifts and seismic activity.
- Tight bend radiuses negotiate obstacles other materials cannot.
- Reel-based fusion joining simplifies otherwise complex routes.
HDPE flexibility makes routing simpler with fewer fitted joints required compared to rigid pipeline materials.
Leak-free Joints and Connections
Butt, socket, saddle, and electro-fusion welding produce full-strength leak-free joints. When performed correctly, fusion forms bonds stronger than the pipe walls themselves.
- Hydrostatic tests validate joint integrity.
- Fusion welding does not require gaskets, sealants, or couplings prone to leakage over time.
- Visible bead formation confirms proper melting and consolidation across the joint.
- Durable, resilient, self-restrained joints without the need for thrust blocks or harnesses.
Permanent bonded HDPE joints avoid potential leaks over piping system lifetimes.
Resistance to Tuberculation and Scale Buildup
The smooth nonporous interior surface of HDPE pipes resists adhering or accumulating particulate, mineral deposits, and biological growth. This maintains flow rates and pressure delivery capacity over long service.
Tuberculation plagues iron and concrete pipes as oxides and scale buildup gradually diminish capacity. HDPE’s low friction coefficient surface prevents this, avoiding costly remediation.
Resilience to Soil and Weather Elements
HDPE withstands exposure to a wide range of soils, chemicals, and environmental conditions making it preferred for buried service:
- Acidic/alkaline solutions have minimal effect compared to corrosion of metal pipes.
- Anaerobic bacteria cannot degrade polyethylene material.
- Freeze/thaw cycles do not damage polyethylene which stays ductile.
- UV radiation including sunlight only affects HDPE surface with no loss of performance.
- Aggressive and abrasive backfill materials will not gouge or scratch polyethylene.
By shrugging off soil and weather impacts, HDPE pipes enjoy long service life in-ground applications.
Cost Efficiency and Value Over Time
The corrosion resistance, reliable joints, and low maintenance of HDPE piping deliver high economic value and cost efficiency over decades of operation.
While HDPE may have a moderate initial cost premium over inferior piping, the avoided replacement, downtime, and loss of service provide a return on investment and superior lifecycle costs for critical piping infrastructure.
Rugged Durability Withstanding Abuse
HDPE’s high tensile strength makes it durable and damage-resistant compared to frangible materials like PVC and brittle iron.
- HDPE suffers no cracking from earth shifts or settling.
- Direct bury installs avoid costly bedding and cushion needs.
- Uneven backfilling does not damage tough polyethylene.
- HDPE withstands abrasion and wear from fluid flows.
By reducing breakage risks, HDPE curtails costly repairs over long service lifetimes.
HDPE Delivers Preferred Pipe Performance
With its lightweight, corrosion immunity, fusion weld joints, and rugged durability, HDPE piping solutions offer unmatched capabilities across essential services. New material technology like HDPE is preferred over outdated but familiar piping.
IFAN
IFAN factory started in 1993. And IFAN has a workshop of 120000 square meters with 610 staff. IFAN can design and produce all plumbing pipe and fitting including PPR, PVC, CPVC PPSU HDPE PEXA PEXB PERT pipe and fitting, brass fitting, brass ball valve, heating system, gas system, sanitary faucets, and hose, In the past 30 years, IFAN has never forgotten his mission-To protect health and safety. And IFAN factory uses the best materials to produce high-quality pipe and fittings with an automatic production line and high-tech quality control machines.