What is an HDPE Pipe?
An In-Depth Look at High-Density Polyethylene Piping Systems
High-density polyethylene (HDPE) pipe has become a major piping material for municipal and utility systems. But what exactly is HDPE pipe and what sets it apart from other plastic or metal pipes? This article examines HDPE to understand its capabilities and why it gets specified for modern piping projects.IFAN factory with 30+ years of manufacturing experience supports color/size customization and free samples. Welcome to consult for catalog and free samples. This is our Facebook Website: www.facebook.com.
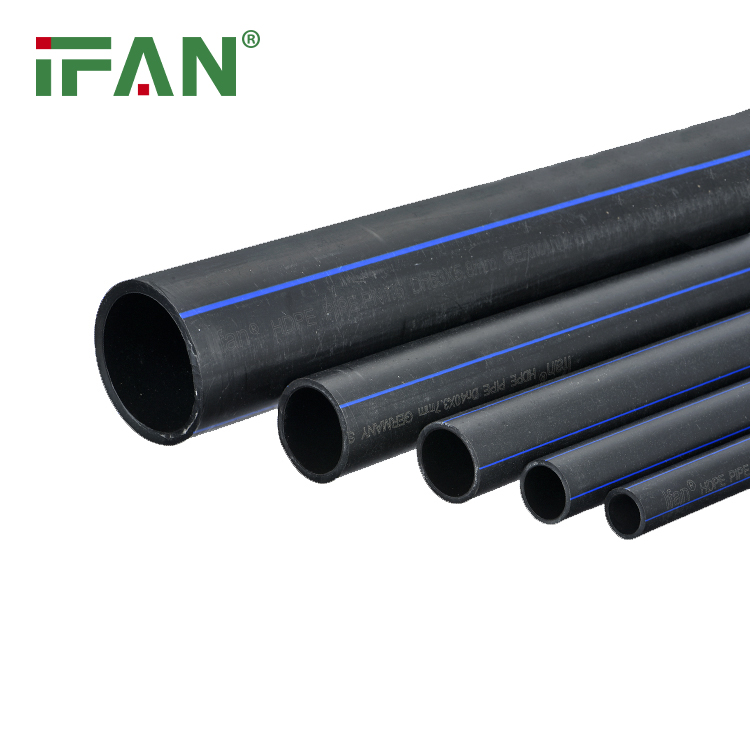
Defining High-Density Polyethylene Pipe
HDPE pipe is a rigid thermoplastic piping material produced from polyethylene resin. It offers high strength combined with chemical resistance and flexibility.
The “high-density” descriptor refers to the HDPE molecular structure which gives it enhanced properties compared to lower density polyethylene used in films and containers.
HDPE gets manufactured into pipes using an extrusion process. Heated HDPE gets forced through a die into a tubular shape as it cools. Straight lengths get cut and butt welded or jointed into complete pipelines.
Key Properties of HDPE Pipe
HDPE possesses properties making it an excellent piping material:
- High tensile strength enables handling heavy pressures
- Hardness provides rigidity and crush resistance
- Chemical resistance allows conveying corrosive fluids
- Low friction coefficient results in good flow rates
- Thermal insulation resists heat gain/loss
- Freeze and fatigue resistance for reliability
HDPE material engineering allows customizing formulations for specialized needs spanning municipal to industrial piping systems.
HDPE Pipe Sizes and Pressure Ratings
HDPE pipes cover a huge range of diameters from 1⁄2 inch up to 65 inches. HDPE can substitute for traditional piping sizes:
- Small diameters compete with galvanized steel
- Large sizes rival concrete and steel pipes
Dimension Ratio standards designate pipe wall thicknesses. Standard DR values range from DR7 for highest pressures to DR17 for lowest. Pressure ratings span:
- 160 PSI for DR9 1⁄2” to 1-1⁄4”
- 125 PSI for DR9 1-1⁄2” to 3”
- 100 PSI for DR9 4” to 65”
HDPE piping can usually match and exceed pressure capabilities of legacy piping materials.
HDPE Pipe Joining Methods
Several techniques produce strong, permanent HDPE pipe joints:
- Butt Fusion – Heating and pressing pipe ends together forms monolithic welds.
- Socket Fusion – Heated fitting sockets melt around inserted pipe ends.
- Electrofusion – Electric coils or wire within fittings fuse to pipe walls.
- Mechanical – Bolted flanges or metal compression bands joint pipes.
These methods allow assembling HDPE into fully fused piping systems suitable for even gas and chemical distribution.
Key Applications of HDPE Piping
HDPE provides an advantageous piping solution for:
- Potable water mains and distribution where corrosion resistance matters.
- Wastewater and sewage transfer in buried drains.
- Agricultural irrigation channels and pipelines.
- Slurry transport for mining operations.
- Landfill gas and leachate collection systems.
- Geothermal ground loops due to thermal resistance.
- District heating and chilled water transport.
- Chemical transfer lines for acids, alcohols, and solvents.
Municipalities, factories, and commercial buildings utilize HDPE piping in place of traditional but inferior materials.
HDPE Pipe Advantages
HDPE provides numerous advantages over other piping choices:
- Corrosion and chemical resistance exceeds even stainless steel.
- Pitting and wear resistant for highly abrasive flows.
- Flexible and fatigue resistant for shifting environments.
- Long pipe sections reduce number of weld joints.
- Impermeable to gas and liquid infiltration.
- Smooth bore improves flow and reduces buildup.
From subzero arctic environments to equatorial jungle villages, HDPE pipe provides decades of reliable service life.
The Rising Prominence of HDPE Piping
HDPE pipe has proven itself across increasingly critical applications from potable water transmission to hazardous chemical containment. In both buried and exposed uses, its light weight, joint integrity, and corrosion resistance provide unmatched capabilities.
As modern pipelines prioritize longevity, economy, and environmental sustainability, high-density polyethylene stands positioned to meet the challenges and supersede outdated piping materials for the 21st century and beyond.
IFAN
IFAN factory started in 1993. And IFAN has a workshop of 120000 square meters with 610 staff. IFAN can design and produce all plumbing pipe and fitting including PPR, PVC, CPVC PPSU HDPE PEXA PEXB PERT pipe and fitting, brass fitting, brass ball valve, heating system, gas system, sanitary faucets, and hose, In the past 30 years, IFAN has never forgotten his mission-To protect health and safety. And IFAN factory uses the best materials to produce high-quality pipe and fittings with an automatic production line and high-tech quality control machines.