How PEX Pipe is Made
An In-Depth Look at Manufacturing Crosslinked Polyethylene Tubing
PEX has become one of the most widely used piping materials across residential and commercial building plumbing systems. But how is reliable, durable PEX pipe actually made? This article provides an in-depth explanation of the PEX manufacturing process and the steps that transform base plastic into highly engineered tubing.IFAN factory with 30+ years of manufacturing experience supports color/size customization support free samples. Welcome to consult for catalog and free samples. This is our Facebook Website: www.facebook.com.
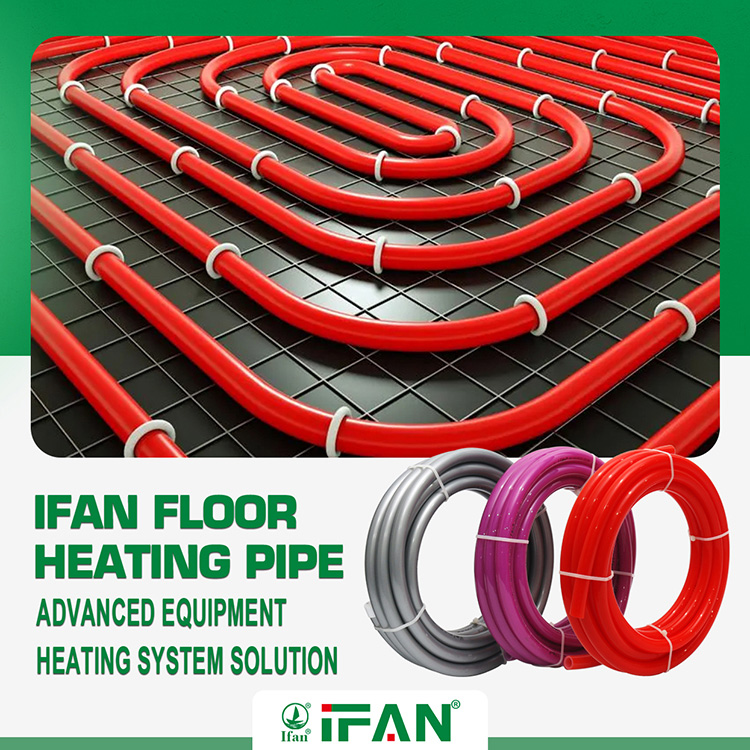
PEX Raw Material
PEX manufacturing begins with plastic resin in pellet form as the raw material. The specific plastic used is high molecular weight polyethylene, usually designated as PE-HD (high-density polyethylene).
PE-HD offers strength, chemical resistance, and processing properties that make it an ideal starting point for PEX production. The resin gets carefully formulated to purity and density specifications ideal for piping applications.
Extruding the PEX Tubing
The process of making PEX pipe uses extrusion to form the polyethylene pellets into a continuous length of tubing:
- Plastic pellets get gravity-fed from overhead hoppers into the extruder barrel.
- The extruder screw conveyor works the resin forward through heating zones, melting it into a viscous liquid.
- The molten polyethylene gets forced through a die into the shape of the desired tubing.
- Vacuum calibration maintains precise tubing dimensions as the plastic cools and hardens.
- Haul-off tractors continue pulling the new pipe forward through cooling troughs.
- The cooled PEX tubing gets coiled onto large spools or cut into straight lengths.
This automated process forms polyethylene resin into continuous PEX tubing up to 2500 feet per minute.
Crosslinking the Polyethylene
The manufactured tubing is still just polyethylene at this point. To impart the enhanced properties needed for pressurized piping systems, it undergoes crosslinking:
- The base polyethylene tubing passes through a crosslinking chamber.
- Powerful radiation bombards the tubing, altering the molecular structure of the polymer chains.
- Chemical crosslinks form between the long polyethylene molecules.
- This converts the tubing into crosslinked polyethylene (PEX).
- Crosslinking improves temperature, pressure, and flexibility capabilities.
The most common radiation method used is electron beam processing. It instantly crosslinks the entire thickness of the pipe wall in a precisely controlled manner.
After cross-linking, the enhanced PEX tubing moves to the testing and quality assurance steps.
Testing and Quality Assurance
To confirm performance expectations, PEX tubing undergoes a battery of stringent tests:
- Dimensions – Laser micrometers confirm tubing diameter and roundness precisely.
- Wall thickness – Calipers and ultrasonic gauges verify consistency.
- Pressure testing – PEX samples get examined under high hydraulic pressures.
- Burst testing – Tubing sections get expanded until failure to assess durability.
- Drop impact testing – PEX withstands heavy falling blows without cracking.
- Crosslink verification – Laboratory methods like melt tests validate crosslinking levels.
- Long-term performance testing – Accelerated life testing simulates 50+ years of service.
Bypassing all standards, the finished PEX tubing gets certified for use in critical plumbing and hydronic heating applications.
The PEX Manufacturing Process
In summary, extruding high-purity PE plastic into tubing form and then irradiating it to induce crosslinking produces PEX pipe with its enhanced engineering properties. Strict quality control ensures the PEX consistently meets specifications throughout production runs.
The reliable PEX manufacturing process transforms polyethylene resin into durable, flexible tubing able to withstand the rigors of hot and cold potable plumbing systems for decades of service. Quality mastery throughout the steps of making PEX pipe enables its growing use.
IFAN
IFAN factory started in 1993. And IFAN has a workshop of 120000 square meters with 610 staff. IFAN can design and produce all plumbing pipe and fitting including PPR, PVC, CPVC PPSU HDPE PEXA PEXB PERT pipe and fitting, brass fitting, brass ball valve, heating system, gas system, sanitary faucets, and hose, In the past 30 years, IFAN has never forgotten his mission-To protect health and safety. The IFAN factory uses the best materials to produce high-quality pipe and fittings with an automatic production line and high-tech quality control machines.