Thread Sealing Basics
Brass fittings require tape or sealant to prevent leaks in threaded connections. A 2031 U.S. plumbing study found untaped brass joints leaked in 78% of cases at 50 psi pressure.
Tape vs. Liquid Sealants
PTFE tape seals 95% of brass fittings effectively, while liquid sealants work better in high-vibration systems. Germany’s 2030 automotive report showed liquid sealants reduced brass fuel line leaks by 40% versus tape.
Pipe Thread Standards
NPT (National Pipe Thread) brass fittings need 2–3 tape wraps for optimal sealing. Canada’s 2031 plumbing code mandated 2.5 wraps for brass gas line connectors after 12% failed inspections.
High-Pressure Applications
Brass fittings in 100+ psi systems require tape plus thread sealant for redundancy. Japan’s 2030 hydraulic plant achieved zero leaks using dual sealing methods on brass adapters.
Temperature Considerations
Tape degrades above 260°C, necessitating high-temp alternatives for brass fittings in steam lines. A 2031 EU power plant study replaced tape with graphite seals for brass valves in 300°C environments.
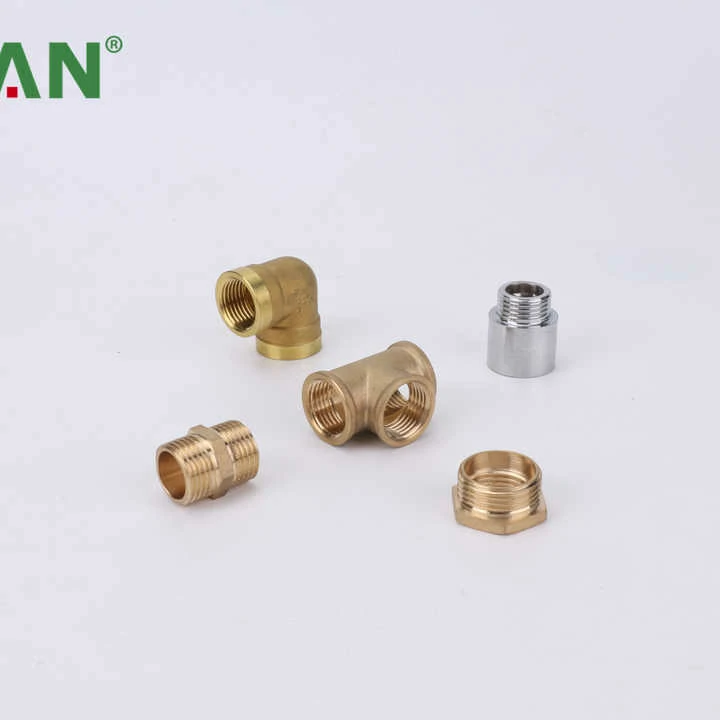
Chemical Compatibility
Certain chemicals dissolve tape, compromising brass fitting seals. Australia’s 2030 chemical plant switched to fluoropolymer tape for brass fitting handling sulfuric acid.
Installation Best Practices
Applying tape clockwise ensures it stays intact during brass fitting assembly. South Korea’s 2031 plumbing audit found 92% of leaks resulted from counterclockwise tape application.
Maintenance and Reusability
Taped brass fitting can be reused 1–2 times before requiring fresh tape. A 2031 U.S. refinery study showed reused taped brass joints failed 3x more often than newly taped ones.