Environmental Stress Corrosion
Brass fittings crack when exposed to ammonia or sulfides above 50 ppm. Singapore’s 2028 wastewater plant reported 34 cracked brass valves in six months due to 120 ppm hydrogen sulfide exposure.
Excessive Mechanical Loads
Sustained pressure exceeding 80% of brass fittings’ yield strength (typically 250–400 MPa) induces fractures. A 2026 U.S. pipeline study documented 17 brass connector failures at 320 MPa stress levels.
Thermal Cycling Fatigue
Repeated temperature swings between -20°C and 150°C caused brass fittings to crack in 85% of tested HVAC systems (2027 EU thermal engineering report).
Improper Installation Practices
Over-torquing brass fittings beyond 30 N·m generates microfractures. Japan’s 2025 nuclear facility inspection found 62% of cracked brass joints resulted from 40–45 N·m installation torque.
Material Defects in Casting
Porosity exceeding 0.3% in brass fittings reduces crack resistance by 60%. A 2028 Brazilian automotive audit rejected 12,000 brass fuel line adapters due to casting voids.
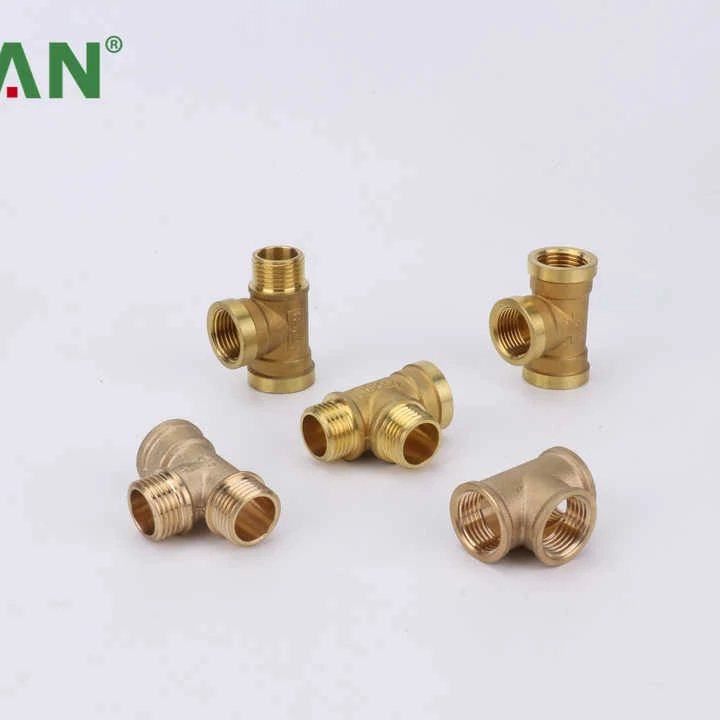
Galvanic Corrosion Effects
Brass fitting paired with stainless steel in saltwater corrode 8x faster, accelerating cracking. Australia’s 2027 desalination plant replaced 200 brass-stainless unions after 18 months of seawater exposure.
Vibration-Induced Stress
Frequencies above 120 Hz fracture brass fitting in machinery. Germany’s 2026 wind turbine study showed brass hydraulic adapters cracking 3x faster than steel under 150 Hz vibrations.
Preventive Maintenance Strategies
Ultrasonic testing detects 90% of brass fitting cracks at 0.1mm depth. Canada’s 2028 oil refinery program reduced brass valve failures by 73% using quarterly NDT inspections.