Can HDPE Be Solvent Welded?
Examining the Challenges and Alternatives for Joining High-Density Polyethylene Piping
Polyethylene pipes like HDPE typically get joined by heat fusion methods. However, due to chemical resistance, HDPE cannot be readily solvent welded. This article explores the challenges of solvent welding HDPE, available alternatives, and when it may work.IFAN factory with 30+ years of manufacturing experience supports color/size customization and free samples. Welcome to consult for catalog and free samples. This is our Facebook Website: www.facebook.com.
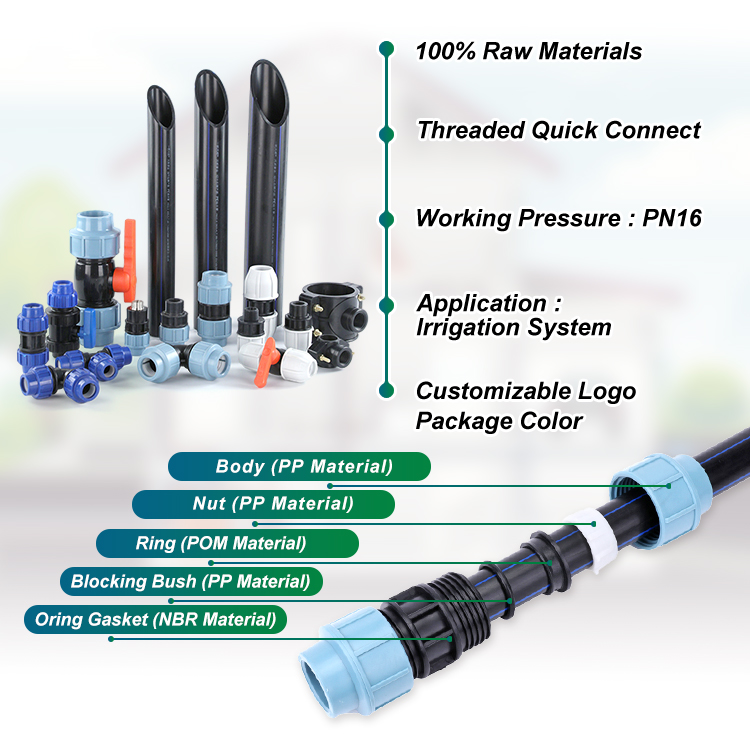
The Solvent Resistance of HDPE
HDPE demonstrates broad chemical resistance thanks to its nonpolar structure which lacks sites for polar solvents to attack. Resistance characteristics include:
- Inertness to acids, bases, and salts across the pH range
- Impermeability to aliphatic, aromatic, and chlorinated hydrocarbons
- Immunity to oils, fuels, alcohols, and moderate organic chemicals
- Resilience against aggressive oxidizing agents like bleach
This resistance makes HDPE an excellent material for chemical handling but prevents dissolving HDPE to fuse joints using solvents.
Challenges Solvent Welding HDPE
The chemical makeup of HDPE prevents effective solvent welding due to:
- Lack of solubility – Common solvents do not dissolve HDPE.
- Slow solvent diffusion – HDPE’s dense structure inhibits penetration.
- Narrow welding window – The brief softening does not persist.
- Low intermolecular attraction – Weak HDPE solvent joints result.
- Olefinic polymers resist polymer chain entanglement.
Together these factors eliminate solvents as a viable HDPE pipe joining technique.
Alternate Joining Methods for HDPE Piping
While solvent welding proves ineffective, several alternate methods produce strong HDPE joints:
- Butt Fusion – Heated pipe ends pressed together creates monolithic welds.
- Socket Fusion – Using heated tools to melt pipe ends into sockets.
- Electrofusion – Electric coils melt the joint between pipes and fittings.
- Mechanical Joining – Flanges, compression rings, and clamps provide tight seals.
By heat fusion or mechanical compression, leak-free HDPE piping systems get installed without requiring solvents.
When Might HDPE Be Solvent Weldable?
Theoretically, at extremely high molar concentrations and/or elevated temperatures, certain aggressive solvents could fuse HDPE joints.
But practical considerations rule this out for piping applications:
- Safety and toxicity risks from volatile, dangerous solvents.
- Extensive surface preparations are needed for wetting and diffusion.
- Very narrow working times before the HDPE re-hardens.
- Inferior joint strength compared to heat fusion.
- Environmental containment difficulties due to solvent mobility.
The costs and dangers cannot justify this route for joining HDPE pipes.
Solvent Welding Other Polyethylene Piping
While pure HDPE resists solvent welding, some other polyethylene or linear polyolefin piping can get solvent welded under the right conditions:
- MDPE – Medium-density polyethylene can fuse with cyclohexane or xylene softening.
- LDPE – Lower-density “squeeze” polyethylene is more amorphous.
- Polybutylene (PB) plastic requires careful surface prep but can be solvent welded.
- Melt blend polymers like XLPE may sufficiently soften for brief bonding.
With trials and prudent safety controls, solvent welding proves occasionally usable for select non-HDPE polyethylene plastics.
Solvent Bonding Considerations and Limitations
A few key factors apply when attempting to solvent solvent-bond polyethylene plastics:
- Limited strength compared to heat-fused joints.
- Acute sensitivity to joint preparation and precise solvent delivery.
- Mechanically inferior wide “weld zones” result.
- Pressure containment relies primarily on extensive clamping.
- Environmental and safety risks demand extensive precautions.
Together these factors confirm solvents do not provide a viable production joining method for HDPE or PE pipe.
Heat Fusion Delivers Superior PE Piping Joints
For joining all polyethylenes, heat fusion produces precision, repeatable, high-integrity joints preferred for demanding applications like gas and chemical distribution:
- Butt fusion eliminates internal weld beads and contamination.
- Electrical fusion consistently heats and melts at precise temperatures.
- Sockets fuse both inside and out for integrity surpassing pipe walls.
- Localized heat and pressure create narrow, incredibly strong joints.
- Fusion bonding preserves chemical resistance and interior bore characteristics.
Contact us to recommend the ideal heat fusion methods for your HDPE or polyethylene piping systems.
In summary, the chemical makeup of HDPE and other polyethylenes makes reliably solvent-welding them impossible. For piping system designers, specifying heat fusion delivers unparalleled performance and safety.
IFAN
IFAN factory started in 1993. And IFAN has a workshop of 120000 square meters with 610 staff. IFAN can design and produce all plumbing pipe and fitting including PPR, PVC, CPVC PPSU HDPE PEXA PEXB PERT pipe and fitting, brass fitting, brass ball valve, heating system, gas system, sanitary faucets, and hose, In the past 30 years, IFAN has never forgotten his mission-To protect health and safety. And IFAN factory uses the best materials to produce high-quality pipe and fittings with an automatic production line and high-tech quality control machines.