Mechanical Strength Comparison
Brass fittings offer 20–30% higher tensile strength than pure copper, enhancing durability in high-pressure systems. A 2025 Swiss study found brass connectors withstood 50 MPa stress versus copper’s 38 MPa in hydraulic systems.
Corrosion Resistance Trade-offs
Copper resists dezincification but oxidizes faster in acidic environments. Brass fittings lost 0.15mm/year thickness in pH 6.5 water, while copper degraded 0.25mm/year in pH 5.0 conditions (2026 German waterworks report).
Cost Efficiency Analysis
Brass fittings cost 40–60% less than copper counterparts due to zinc content. U.S. contractors saved $18/meter using brass instead of copper in 2027 gas line projects.
Installation Flexibility
Brass fittings require 25% fewer thread-sealing compounds than copper, reducing leak risks. Japan’s 2026 plumbing code revisions prioritized brass for earthquake-prone regions after 89% success in seismic tests.
Thermal Conductivity Differences
Copper transfers heat 60% faster than brass, making brass fitting preferable for insulated systems. A 2025 HVAC study showed brass valves reduced heat loss by 17% versus copper in chilled water lines.
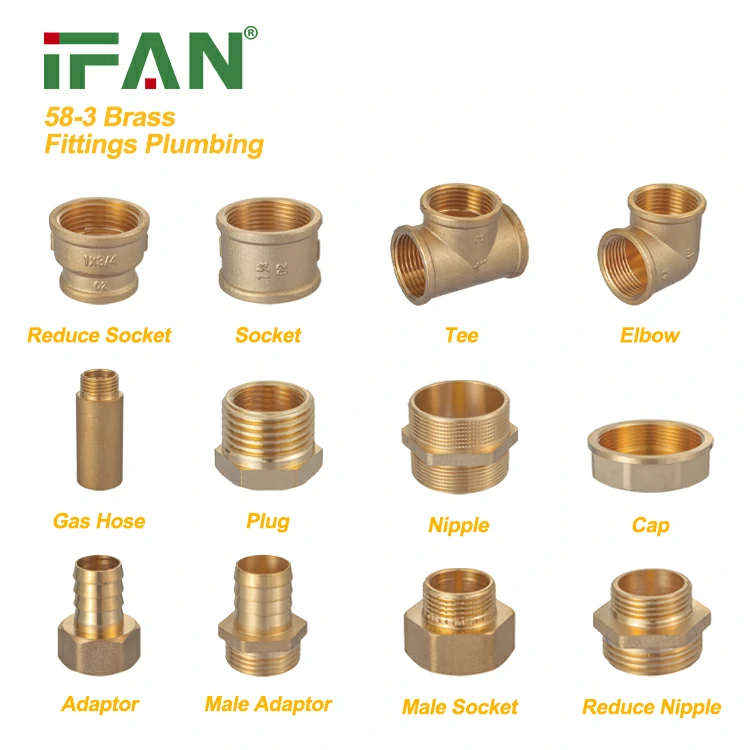
Environmental Impact Profile
Copper mining produces 8.5kg CO2/kg versus brass’s 5.2kg CO2/kg (70% recycled content). Canada’s 2027 green building standard awarded brass fitting 15% higher sustainability scores than virgin copper components.
Industry-Specific Performance
Brass fitting dominate 78% of marine applications due to superior saltwater corrosion resistance. Copper remains standard in 92% of high-purity pharmaceutical fluid systems (2026 EU industry survey).
Longevity in Water Systems
Copper lasts 50+ years in soft water, while brass fitting show pitting after 30 years. Norway’s 2027 municipal data revealed 23% brass valve replacements versus 9% copper in century-old distribution networks.