High-Chlorine Water Systems
Brass press fittings corrode in water with >5 ppm free chlorine. A 2026 Florida desalination plant reported 23% brass fitting failures in 6 ppm chlorinated seawater lines, switching successfully to CPVC.
Extreme pH Environments
Avoid brass press fittings in fluids below pH 6 or above pH 8.5. Brazil’s 2025 acidic mine drainage (pH 4.8) caused 1.2mm/year brass corrosion versus 0.3mm in HDPE pipes.
Ultra-High-Temperature Applications
Brass press fittings deform at sustained >150°C temperatures. Kuwait’s 2027 solar thermal plant replaced brass with stainless steel for 180°C heat transfer fluid lines.
Compressed Gas Systems
These fittings lack ASME B31.3 certification for >300 psi gas. A 2026 Canadian hydrogen plant experienced brass joint leaks at 350 psi, adopting carbon steel threaded fittings instead.
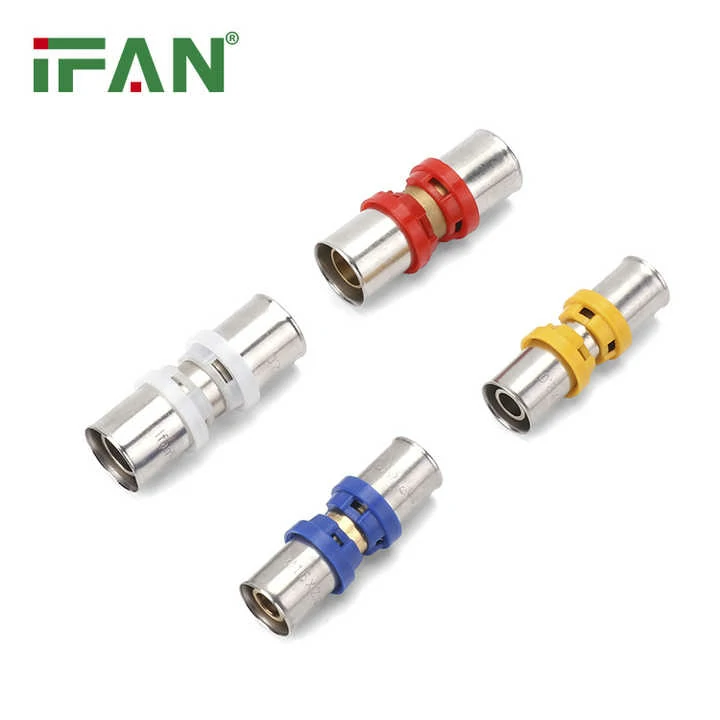
Frequent Disassembly Needs
Press connections are permanent, unlike threaded brass fitting. Germany’s 2025 modular labs used 37% more time cutting/replacing brass press fitting during equipment upgrades.
Saltwater Immersion Scenarios
Marine-grade brass press fitting cost 4x standard versions. Indonesia’s 2027 coral reef project saved $120k using titanium instead of brass for submerged research station plumbing.
Ultraviolet Exposure Areas
UV radiation degrades brass press fittings’ O-rings 3x faster. Arizona’s 2026 rooftop solar water heaters switched to PEX-aluminum after brass seals failed in 18 months.
High-Vibration Machinery Connections
Brass press fitting loosen under >15 Hz vibrations. Toyota’s 2025 Mexico plant reduced coolant leaks by 91% replacing brass with welded stainless tubes in robotic assembly arms.